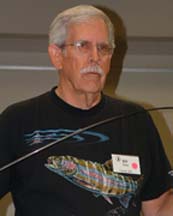
BD Ehler is a retired Pharmacist who started fly fishing in the 50’s. He learned to tie flies and began to repair his own rods. He built his first rod from a kit in the 60’s, became interested in creative rod work and joined RodCrafters in 1974. He met Dale Clemens and others who were developing creative concepts in custom rod building at National seminars. Thread art was limited at the time and caught his interest.
He developed numerous patterns of crosswraps and contributed many of them to Custom Rod Thread Art, published by Dale Clemens. He is also well known for sharing his experience with other rod builders and continuing to teach others to build custom rods. He says that the best part of custom rod building is the friends that he has made over the years. Almost every rod builder has referred to Custom Rod Thread Art at one time or another. Without unselfish builders like BD, custom rod builders would not have such great resources available to them.
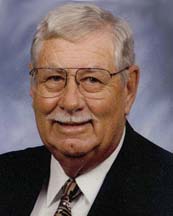
Over the years Pat has fished extensively in fresh and saltwater, often traveling to many places that normal people never get an opportunity to fish – such as Greenland. His fishing under extreme conditions and at remote locations has resulted in a deep appreciation for fishing rod reliability and performance. And, that building your own custom rods is the best way to satisfy this requirement.
Pat has come in contact with many types of fisherman and rod builders as the past President of the Montgomery Bass Masters, one of the first Directors of the Alabama Federation of B.A.S.S., and the Director of Seminars for RodCrafters, and the Conclave Director for the Custom Rod Builders Guild.
He is perhaps best known in rod building circles for creating
realistic fish image inlays using feathers and in the construction of high performance rod handles. More recently, he has expanded his feather inlaying to included southwest Indian art and snake skin inlays.
Excelling in the craft of custom rod building takes time and effort. Pat readily admits that his “first attempts were not too good.” With the help and support of Guild members, he has been able to hone his style, and pass-on the techniques. Pat encourages rod builders to try thread or feather art, weaves, grip inlays, or various combinations as a way to visually separate custom rods from mass produced production rods. These artistic additions in no way hamper rod performance and often result in educational discussions about the merits of custom rods. “Almost anyone can recognize quality and attention to detail – even from across the room.”
As one who follows new developments in rod building, Pat is happy to note that “the past few years have seen great advances in custom rod building including the quality of rod components and the publication and availability of custom rod building techniques and methods.” He believes that the exchange of rod building information using the internet may be one of the most important recent achievements in custom rod building.
That being said, however, Pat views membership in the Guild as paramount for making friends, learning new methods and techniques, and sharing information. In attending several regional meetings each year, he has been able to keep in touch with fellow crafters, develop relationships with suppliers and wholesalers, and participate in in-depth discussions regarding the craft. “Often having someone to listen to your ideas and concerns is the custom rod builders’ greatest asset.”
With 33 years of rod building under his belt, Fuzz Morgan has witnessed countless changes in the design, construction, and artistic quality of custom rods. Primarily a bass fisherman, his rods reflect the influence of the diverse rod builders he has met and befriended through the Guild. He credits his progress on getting to know a variety of builders, exchanging ideas, and learning something new from everyone. “Just ask and you’ll get some answers.” Over the years, discussions on blanks, guides and their placement, handle design, and decorative trimming have helped Fuzz create rods that are not only highly technical in their design – they are real eye
catchers!
As a grandfather, Fuzz understands the importance of passing on his
information gleaned over time. At Conclaves and regional meetings, you will find him demonstrating personal techniques and readily explaining new ideas and established concepts. His presentations at Nashville, Shelbyville, and Atlanta have helped both newbies and the accomplished better their craft.
His reserved demeanor belies his excitement in discussing fishing rods. Strike up a conversation and you will soon find yourself immersed in a discussion detailing the merits of a Lamiglas blank, inside tips on mounting texalium tubing, or his dream of the perfect 7 ½’ flipping stick. “Want a sensitive rod? Just pair a no-stretch braided line with a rod built using a well-designed blank, the new guide concept, and a woven graphite handle.”
You will quickly be able to identify his current rods by his feather designs of bait. He builds these images freehand – no patterns, no
stencils, no layout. What you will find is very realistic depictions of jigs, worms, hard bait, spoons, and flies. Fuzz gets his design ideas from real life, magazine articles, and product catalogs. “A tubing handle is great place to inlay images. It’s a great way to differentiate your rod from a factory rod. People want to pick up a rod with an interesting design – especially feathers.” No doubt about it… Fuzz builds a rod that is highly functional and fun to look at!
Bottom line – Fuzz builds rods because “it just feels good to catch a bass on a rod you built yourself.”
WE ARE ALL ARTISTS
The dictionary defines Art as a creative skill in painting, sculpture, music, poetry, etc to produce works of beauty. I have always considered cross wraps, weaves, and inlays, (foam and feather) as works of art. I also include the art of making a bamboo rod in the same category.
There was a time not long ago when some people referred to this work as cosmetics, a term I strongly objected to and with the help of Cam Clark we got the word eliminated from use at seminars. As rod builders, we want to make the best rod possible, a rod that is sound and functional and technologically superior to any factory or store bought rod. This is our primary goal, but we also want to make the rod as as attractive as our creative ability will allow. This is where wraps, weaves, and inlays became
important to help us produce not only a great rod, but a great looking rod.
I came to recognize the beauty of fishing rods when I saw my first decorative rod years ago. I can still recall the very first rod I made and that it had a wooden handle. Not content with a plain looking handle, I burned sections of the wood on the kitchen stove to give it an antique look. Very soon after that I moved on to work with cork. I continued with cork for a while, but when fine cork became scarce I switched over to foam grip materials.
In the early eighties I came across a picture of a saw tooth grip on the cover of a Rod Crafter Journal created by Charles Alexander. I thought at the time it was the most beautiful grip I had ever seen and knew that I had to make that grip. However, to my great disappointment there was no explanation or instructions in that article about the grip. Little did I know at the time that they had done me a great favor because I had to rely on my own initiative to figure out the “how to”. This lesson served me well later on with other projects. After making my first saw tooth grip, I wrote the instructions and with diagrams, sent it out to the Rod Crafter Journal.
A few months later another rod builder from Chicago sent an article describing his method of doing the same grip. We became good friends because the two of us shared the same enthusiasm for the artistic side of our craft. That person was the late and great Emil Baggetto.
After making many more grips with the saw tooth I knew it was time to move on and I became interested in working with split rings to make all kinds of new designs. After a long time working with this technique I got to the point of exhausting all the ideas I had and once again I knew it was time to look for a new outlet.
Looking at the Clemens catalog, I found a thin black foam sheet in the back of the book. I never learned what use this had for anyone, but decided to order it and that was the beginning of my work with inlays. I cut the sheet up in different shapes and then glued them into the grip. To my great joy the thing worked. The sheet though was much to thin, but Dick French made a thicker sheet for me and that proved to be perfect for my needs and that became the Bernie sheet in the Clemens catalog. I began to make pictorials
of fish, fisherman, boats, and many other things and could not wait to show off my new creation to the rod builders at the seminar. Emil Baggetto was also working on the very same thing and we both showed up at the seminar and each one of us was surprised that we both had thought of the same thing.
I never learned his technique, but I suspect that he may have been working with squares, a method that I cannot do because I do not have a shop. I do all my work in my apartment, where I do not want to make any unnecessary dust and dirt.
What intrigues me the most about pictorial inlay is that it is eclectic. The ideas can come from many sources like newspapers, magazines, book covers, sports insignias, and even cartoon characters. Any thing you can imagine that may look good on a grip can be done within the confines of the diameter of the grip.
When you combine the inlay grip with a complimentary cross wrap or weave you have a true work of art.
Bernie Cohen
Rod building is a skill I practiced early in life as a necessity if I wanted something other than a cane pole. I guess my first rod was not built or constructed but more put together with a cane pole and baling wire. My first rod was built in 1954 with one of the first fiberglass rods that I had ever seen. My father needed a new fly rod so I told him if he would buy the parts I would make it for him. By the way, still have the rod. During the period from the late 50’s until the late 70’s the tasks used in rod building were self learned because in most areas no one else was building rods. In the late 70’s I heard about RodCrafters.
Dale Clemens set-up a meeting in Huntsville Alabama, which was close to where I lived. I registered for the meeting and for the first time in my life I met with other rod builders. The things we talked about just blew my mind and I was hooked. The next year I attended two meetings and the rest is history. In the past 30 years I have attended meetings all over the country and have had a chance to meet, not some of, but the greatest friends a person could have.
Don has unselfishly shared his research findings with rod builders for years at his own expense. His fascination and research with the physical characteristic of rod blanks has resulted in many rod manufactures adopting and using his recommendations in their manufacturing processes. He is a talented teacher and gets great satisfaction in showing and demonstrating how to get the most performance from every type of rod blank.
Don is also a very inventive engineer. If he needs a tool, test equipment, test stand, or any device that’s not available on the market, he manufactures it and shares it with his friends and others. He has made a number of tools that he has given me e.g. spine finders (4 different types) guide placement charts, weaving tools, mandrels etc.
But the most important thing is that Don is a reserved person who gets great joy out of sharing his methods and techniques, but does not seek any recognition or financial gain. He is indeed a rare and fine person and hopefully our young and future rod builders will benefit from his research and sharing.
– Pat Vinzant –
Don & I first met about 10 years ago at a RodCrafter gathering in TN. He was working on a new method of weaving using a loom type mechanism. We visited about the loom concept and reviewed his prototype ideas. Don was very easy to talk with and receptive to comments about his ideas. There was an instant friendship that developed from the first conversation, which is quite typical of Don. It took about 3 years for Don to complete his loom project with 4 or 5 prototypes started and dumped before his loom was finalized. Dick French also worked with Don and the loom became available through Clemens Custom Tackle.
Don has been building custom rods for many years and had already become very good on cross wraps and weaving. He had developed the ability to create new cross wrap designs, like names repeated up the rod. His talent in weaving expanded with the use of his new loom to the point where he could weave a fish without the use of a graph, chart or left list.
Because of Don’s love for teaching, his lifelong profession, and his natural curiosity about how things work, he started putting his retirement energy into rod building. He has developed several types of spine finders through the years and also the Morton Chart for guide spacing which he continues to modify as his knowledge of rod blanks has expanded. His abilities have resulted in a large variety of tools being used in rod building. His rod set up regarding guide spacing and orientation on the rod blank has come from years of experimenting along with his mathematical background.
Don has used his teaching skills all over the Nation to help rod builders better understand how a rod should be set up to give the greatest amount of sensitivity and effectiveness to their rods.
Don is a family oriented, humble man who loves to share his vast knowledge bank with his friends. Once you have spent some time learning from Don you not only become an admirer of his abilities, but to him — you are now part of his family. Personally, Don & I have shared time in a boat in both Alabama and Kansas, testing rods of course! We have shared travel time together going to seminars in MN and FL. We have visited on many different subjects through the years from health issues to rod building topics. Consequently, I have developed a great affection for this kind, brilliant, humble, sharing man. In short, I have been Mortonized!!!
– B.D.Ehler –
I met Don at Rod Crafters years ago and since that time we have become close friends. He has given so much to our craft and to so many of us who build rods. He is always working on something that will enable us to get the best performance out of any rod we build for our own or customers.
One thing that I remember to this day is the first time I ever visited Don at his shop. I spent the day with him and left there with my head spinning from all the things we did and talked about. He shared a lot of things that day that I put to use to this day. The knowledge he has and shares with everyone is amazing. The only thing is you have to prod him a little to get him to talk about spine ,rods, etc.
I think Don is truly one of the LEGENDS of rod building and I cherish the friendship Elaine and I share with him and his wonderful wife Carolyn.
May we float the DUCK many more times together and catch a lot more fish.
– Fuzz Morgan –
Fairly new to the rod building craft, I built my first rod in May of 2006. Began with a couple of kits from Cabelas and was less than satisfied with the look of the cork included with the kit. It was great practice and gave me an idea of how to assemble a rod. I had turned a few pens and enjoyed wood turning and thought that wood had some possibilities for rod building. I really had no idea what I was doing and turned a couple of plain wooden grips, without segmenting or decorations.
After I learned of the Rod Guild and The RodCrafters Journal, I joined later that year. The first issue I received had an article on making wooden checkers by Bob Hasbrook. I thought that it was interesting and gave it a try. After that I was hooked. Fortunately, several rod builders have taken me under their wing. Joe Emig introduced me to segmented turning and showed me a couple of techniques to make a better grip. I also came across Ron Walter and he gave me encouragement and has been very good about teaching me the proper way to assemble a rod. Billy Vivona befriended me and has been great about feeding me ideas and helping me find a way to build a better grip. There are many others that have helped me along the way, too many to list. I have never met a group that is as helpful and as caring as I have in this organization. I am learning every day and hope some day to be able to share what I have learned.
Doc Ski, aka James Labanowski, known both to the world of sport fishing and rod building was born and raised in California. Doc received his nickname because he was a hospital Corpsmen in the US Navy. He retired in 1985 as a Chief, which was no small task in itself.Now residing in Oxnard, he officially opened Doc Ski Rods. Even prior to retirement Doc had been written up in several sport fishing magazines and papers for his unique style with thread art on custom fishing rods. Also recognized in the industry for his fishing abilities and tackle innovations, Doc is renown for modifications in long range tackle and one of the most successful Wahoo lures on the market. Using golf as an analogy, Doc tries to explain that each rod has a purpose for fishing just as each club has a purpose for golfing. Having the correct tool means more success in any venture.
Doc has been wrapping rods since the age of eight after being taught the basics of replacing guides by his father. He has received advice and guidance from such well known people as Jean and John Harrington of Harnell fame and Leon Todd (owner of CalStar Rods). Doc was first recognized for his thread artistry using techniques such as cross wrapping diamonds, chevrons, box patterns and his recent work with the tiger wrapping techniques published by Scott Throop.
Doc Ski has become world famous for his intricate weaving designs. His weaving artistry has been compared to painting with thread. Doc can create a life-like action picture of a Tuna with a water splash at Alijos Rocks jumping to take a kite bait. He has also weaved a perfect replica of the Purple Heart Medal in picture like detail. Many of his designs can use up to 600 threads. Doc exclaims that the possibilities of weaving designs are endless. These are well demonstrated by his sample cases of over 500 different designs. An Individual weaving design may take over 40 hours to complete and yet be only about one and one-half inches long.
Doc has dedicated himself to passing on his art forms to all who would like to learn how to do them. Sharing his expertise now is an endeavor Doc finds more fulfilling than creating his thread art originally. Doc Ski is often found at trade shows in California where he demonstrates his artistic talents and teaches his craft to others.
Recognized by the Guild at the Conclave in 2007 as one of the Legends of Rod Building, Doc feels this to be one of his most valued accomplishments. He says, “Having ones peers recognize, not just contributions to the art and craft, but the teaching and sharing of a new generation, I can’t think of a more humbling honor”.
For the most part Doc has retired from the commercial end of custom rod building, yet he remains active in developing new techniques, patterns and charities he has been involved with for some time.
My family’s cottage at Deep Creek Lake in Maryland is where my obsession began. My father, my uncle, and I fished the lake every weekend. My passion for fishing has grown ever since.
My rod building started after a few trips to the Outer Banks. The locals had these “custom heavers” and could outcast any rod I owned! These guys could cast 100 plus yards; reaching the outer sand bars needed to catch the most spectacular Redfish. All I could do at that time was watch! I looked into buying my own heaver, but could not afford one. I returned home and started to research rod building. After purchasing Dale Clemens’ rod building book and through trial and error, taught myself how to build rods. I built a few rods and my family and friends really liked my work. They put in their “requests” and started to building for them.
I’ve been building rods for approximately 12 years. My first were surf rods and quickly replaced all my factory built rods with customs. Starting with rod repairs and taking custom rod orders for a “high end” fly fishing shop in Pittsburgh, Pennsylvania, my customer base began to build quickly and business expanded. Because of my wide variety of fishing, I build rods for trolling, fly, noodle, float/center pin, surf, spinning, casting and everything between.
My focus is on the quality of my work. I take great pride in the rods I build and pay great attention to detail. I enjoy building custom rods and feel privileged to be part of the Custom Rod Builders Guild.
I was about 10 years old when my father first took me freshwater fishing for Bluegill. From that day forward I knew I was hooked. As a teenager, my passion for fishing grew and I started tying my own flies to catch Large mouth Bass at the local lakes. I continued to fish as much as I could into my adult years and had interest at one point in learning to build my own fishing rods. I briefly looked into it but between shift work as a California Highway Patrol Officer and raising a family I just couldn’t find the time.
Then fate struck on Friday the 13th 2003 when I was en route to motorcycle training and got struck head-on by a truck that crossed the centerlines. My nearly 18 year career abruptly came to an end after a two-week hospital stay and months of numerous surgeries. While attending therapy for my left hand and arm I began researching the craft of rod building.
I first started building ultra-light freshwater rods which not only occupied my free time but also acted as a means of therapy. The intricate thread work helped tremendously in getting the flexibility and feeling back in my fingers. I bought the books by Dale Clemens, the videos by Doc Ski and spent a week with a rod builder in Alabama named Lee Selman. My interest in rod building grew into an addiction and eventually into the small business it is today.
My favorite rods to build are freshwater bass rods and the heavier saltwater live bait and trolling rods. I try to make my relationships with my customers a very personal one and like to feel my attention to detail shows in each rod I build whether it’s simple or intricate. I’m also very proud to be a member of the Custom Rod builders Guild.
– Tom Greek – Founder – Custom Rod Builders Guild
Tom was a big, but unimposing man. A person whom everyone would like to be around. He loved to talk about “his Guild”, and the passion he had for nurturing it into a national, if not a world-wide, network of professional rod builders. The first 50 members were charter members and that list of builders is a list to behold! A true craftsman, who enjoyed working with his hands, with tools, and a master fly rod builder and fisherman, Tom believed that there was a need for professional rod builders to be surrounded by others to spread the craft from hobbyist to those who could potentially make a living building rods. He taught rod building in his home town of Nashville, TN, thru FFF groups and others. He would work with groups or one-on-one to teach others what he knew. As his professional career as an insurance broker grew into a very large business in Nashville, taking much more time than was in a day, he began to lose control over his dream for the Guild. His ultimate dream for the Guild was that it would provide for some of his retirement income…. Retirement never came for Tom. A few short years later, it became clear that the Guild would not succeed if it were not taken to a different level, that being of a member-owned non-profit.
Like you, I once was a novice and knew no one in rod building. I asked Mark Cook about the Guild and Tom Greek in the spring of 2000. Mark said he was a great guy, and that I should join the Guild then attend the Conclave II in Nashville. I did so as member # 68, just missing the cut-off for the original membership founders. As I arrived at the hotel, there was this big guy with a smile on his face and a out-stretched hand welcoming me to the Conclave. I, of course, felt a bit intimidated to meet him first before any other builders, as I had only a few rods built by then and was still learning. He was quick to introduce me to others and seemed to be everywhere at the Conclave.
Before that Conclave was over, Tom had invited me and others to go to dinner and share experiences with everyone. People like Bruce Young, Doug Weber, Bob McKammey, Todd Vivian, Paul “Coach” Bagby, Garry Loomis, Neal Hall, and others went along. What a treat for me!
Each Conclave since, Tom greeted me at the registration desk, and we repeated the dinner deal, the last time was in Minneapolis August 2007.
My last long visit with Tom was at Conclave VIII in Minneapolis. Tom had a vision for the Guild that now has taken another direction from his original plans. He was not at all sorry for the changes but still lamented that his original plans could not be implemented. He also was very proud that the Legends of Rod Building was being kicked off at CVIII. Some of the Legends had been requested to assist in building a community rod that was later auctioned as a fund raiser. Tom had built without the use of any power tools the most exquisite inlayed wooden box for this special 4 – piece Legends Fly Rod. He was so proud of his accomplishment and the way the rod perfectly fit. Hundreds of hours of labor went into this beautiful Legends Rod, and Tom as the guiding force behind it being built. That rod raised over $3,000 at auction during Conclave VIII and was purchased by Bill Batson, Batson Enterprises. The rod hangs proudly in Bill’s office in Squim, Washington.
Tom Greek was a true craftsman, a master rod builder, with a passion for fine woodworking. While others knew him better than I, I will never forget his warm friendship. He certainly is a true Legend.
Kris Kristufek
Thomas Richard Greek born September 25, 1944; Died December 31, 2008. Every aspect of his life and character will be missed greatly. Tom was a caring husband, father, grandfather and friend, who devoted his time and talents to those he loved. Tom was a master artisan, whose creations in wood, rod building, and fly tying will be remembered and appreciated by all who knew him. An avid outdoors man and founder of the Custom Rod Builders Guild, his love of fishing will endure through his friends and children. Thomas Greek is survived by his wife, Elizabeth (B.E.); his children, Michelle, Thomas, John and James; and 6 grandchildren.
Charlie Sexton has been building custom fishing rods for over 30 years. He was introduced to the craft through a paperback book from Gudebrod in 1975. Subsequently he read two Dale Clemens books on rod building and an instruction book on thread art. In 1980 he joined The Rod Crafters’ and attended his first rod seminar in 1982. Since then, Charlie has attended every Rod Crafters / Guild seminars except two. In 1983, Charlie showed Dale Clemens some wooden reel seat inserts he had made and Dale asked Charlie to demonstrate. Since then, Charlie has tried to demonstrate something new every year. His friend, Bernie Cohen, has named him the “Rube Goldberg” of rod crafting for his continuing efforts in lathe tool design and miscellaneous gadgets to aid the rod crafter. Most of his innovations are made from parts most guys find in their garage.
Charlie continues to improve his skills while teaching his Family and friends. His grandson, Chaz, has attended seminars and assisted in demonstrations. Another grandson, Dakota, has just built his first rod with Charlie. Charlie has also held small seminars for friends who are eager to learn the craft and share his enthusiasm.
Charlie retired in 1986 after flying for 32 years with Eastern Airlines He was married to the late Mary Sexton for over 50 years and has two grown sons and four grandchildren. In addition to rod building, Charlie is an avid golfer enjoying a 12 handicap and occasionally scoring his age!
Rich grew up in Naples, Florida, and as a boy often spent more hours a day fishing from the local pier than he did at home. He built his first fishing rod at age 12; an old Fenwick blank with a one-piece cork foregrip and an electrical tape-wrapped clothesline rear grip. The wrapping was done by sticking the butt in a shoe, sewing thread spool in one hand while twisting the rod with the other. Truly “old school” rod wrapping! Thirty some odd years later, he is still building rods, but with nicer tools and equipment. Rich is just a hobby builder these days, making rods for himself and friends, and occasionally donating rods for silent auctions that benefit worthy causes. Rich graduated with a degree in Forestry from the University of Florida. While attending college, he built and repaired fishing rods at a tackle shop in Gainesville. Rich currently works as the Fire Training Officer for the Florida Division of Forestry stationed in Brooksville. He still enjoys fishing, and competes in quite a few saltwater inshore tournaments in South Florida. He finished well enough in a few big tournaments to qualify to fish the IGFA Inshore World Championships in both 2008 and 2009.
Rich became serious about thread art with the help of an early mentor, the late great Sam Price. Sam was a master rod builder at Naples Sporting Goods, and was Rich’s “sensei” for many years. With Sam’s occasional help and tips, Rich worked his way through many of the patterns picked up out of Dale Clemens’ books. At this point, Rich only concentrates on cross wraps.
After years and years of wrapping rods by hand, he finally broke down and bought a machine about 3 years ago. Recently he purchased Billy Vivona’s book on Decorative Wraps. With some of the tricks he learned in that book, and some advice by master rod building friend Robby Turner of Surf and Turf Custom in Naples, he feels like he finally “turned the corner” on thread art, and is now truly happy with his work.
As a 65 year-old, retired teacher from Edgerton, Wisconsin, Ron lives with his special wife, Mary. Together they raised three grown children who have blessed them with seven grandchildren. Mary is the controller for a large structural steel fabricator while Ron taught high school earth science, biology, physical science, and physical education for 37 years while coaching several sports. At that time when one of his student athletes tried to call him “Wally” Ron retorted,”Mr. Wally to you, fella!” Thus mrrwally eventually became his e-mail name. mrrwally@hughes.net The second r is for Ron.
The final ten years of Ron’s teaching was in an “At-risk” program for troubled kids. This assignment was his most rewarding time in education. The slogan for his one room school house away from the regular high school was, “Where Every Student is a Favorite!” As part of that program students who were present all week and had completed all their work at an acceptable level, were able to build custom fishing rods on Friday afternoons as a reward.
Mr. Wally started rod building in the early 1970’s when he needed to repair a loose guide by using 4 lb test fishing line. He didn’t know how to finish the wrap until a fly fisherman showed him how to pull the line under using a pull through loop. He soon discovered Fiberglass Rod building by Dale Clemens. Shortly thereafter, Ron joined “RodCrafters” as a professional member. Then came Advanced Custom Rod Building, and Custom Rod Thread Art. Rod builders in the Mid-West were unusual at the time and without the aid of computers back then, Ron never met another rod builder until joining the Guild in 2003. At the North Central Conclave in Breezy Point, MN he met his first builder who just happened to be B.D. Ehler!
Soon Ron became a regular at national and regional conclaves and has traveled to North Carolina, Pennsylvania, Texas, Tennessee, California, Washington, Minnesota, Illinois, and Iowa to attend various workshops and events. He was the secretary for the Guild for a while and is probably best known for being the editor of the “RodCrafters Journal” for several years.
Ron’s business, “Pike Lake Custom Rods” (customrods.org) was started in the summer of 2004. He continues to teach rod building to kids through the Guild program, “Pass It On” in conjunction with Big Brothers Big Sisters, Boy Scouts, Optimist Clubs, and others. In fact he has completed over 50 workshops with various youth groups since he retired.
Ron says that he Guild has opened many doors for him and he can truly say he rarely meets a rod builder he doesn’t like or respect. Rod building can be a wonderful hobby or even a business and the Custom Rod Builders Guild organization is just one of the ways rod builders can share tips, tricks, and techniques while building wonderful friendships all over the country and the world.
Fishing is in my blood, especially sea fishing from the beach. During my youth you could find me fishing from one of several beaches located on the East Coast of England, either in Club competition matches or simply enjoying being out there fishing. From the many visits to tackle shops at the time, I always asked myself “Why are all rods finished in black?” So at the age of 14, with my late father, I went off to the East End of London and a cane merchant where I purchased a 25ft to 30ft Burma Pole. From this length of whole cane I built my first fishing rod, an 11ft beach rod finished in red and black. This led to a Saturday job in a local fishing tackle shop, followed by a full year in the shop doing the shop rod repairs before entering public service. Throughout my 30 years of service I kept my hand in repairing & building rods for all disciplines of angling.
Retiring 13years ago it was time to change direction in my life and with the support of Wendy, my wife, an opportunity to advance my rod building skills. Plus I wanted to learn more about thread art, specifically working with metallic threads. There was only one place to head for – the USA and membership of the Rodcrafters Assoc. of America. Attending National & Regional Seminars of Rodcrafters in Allentown, PA; Kissimmee, FL; New London, CN, then, following the merger of Rodcrafters with the Custom Rod Builders Guild, attending Conclaves in Atlanta, GA, Minneapolis, MN and Allentown, PA. Along the way I have been privileged to meet some of the greatest custom rod builders of this era and I could fill several pages with names and memories. A few hold special places. The late Cantwell ‘Cam’ Clark, for his warm and generous welcome for Wendy & I on our very first visit, his willingness to share, his humour, plus with his cardboard tube and ropes he taught me the basics of weaving. “Doc Ski” the master of weaving and so much fun when out fishing even if I can’t cast!! Al Goldberg, angler, rod builder, master chef – a natural, not forgetting he is a most generous host. Then, for me, the most inspirational rod artist I have shared time with, shared skills with, laughed with, fished with and cried with – Bernie Cohen the rod builder who developed the “Bernie Wrap” for stripe bass rods. There are many more, too many for this page, just to let them know and say “Thank you” – TLC; Kel; Sam; Kris; Buddy; Jessie; Curt; Dick; Todd; Walter; Doug; BD; Joy; Jack J, and all other members I have enjoyed sharing time and skills with.
Around the same time as I retired I also qualified as an Angling Coach, “Licensed” to coach & tutor sea shore fishing and UK freshwater fishing. This qualification has opened many doors and unbelievable opportunities. For the past 7yrs I have travelled annually to coastal regions of the Kingdom of Saudi Arabia coaching competitive shore fishing skills to potential Team members of Saudi National Teams. The picture featuring my Saudi visits shows me being introduced to the Amir of Jizan, Prince Mohammed bin Nasser bin Abdulaziz, at the Harrad (Parrot fish) Festival on the Farasan Islands in the Red Sea. These coaching visits are part of a much larger sports youth welfare & development project covering 50 to 60 different sports.
Back to rod building. Those early years at seminars were mind blowing, so much to learn the brain couldn’t take it all in. The long flights across the Atlantic were time to unscramble some of the scribbled notes, read the handouts and put the lot together ready for the next rod building project!. Slowly the tide turned and I started sharing and leading the seminar workshops with some of my skills. One day in the UK I was shown some key-rings shaped as the three main styles of fishing reel – my visualisation said “These need a fishing rod”. The mini-custom built rods were born. Late 2006 I was approached to work with golf clubs for the 2007 International Pairs World Golf Championships. Within the logo of “International Pairs” the “I” is the image of a golfer hitting a drive off the tee. This image I created into a weave and worked onto the pair of golf clubs presented to the 2007 World Champions. 2007 was a milestone in my Custom Rod Building career. Conclave VII honoured me with a nomination of “Legend of Rod Building”. My peers placed me alongside Custom Rod Builders who I look up to, whose skills I aspire to emulate.
Attending the Seminars is probably the most significant benefit to be enjoyed by any member of either the former Rodcrafters or the Guild. Meeting, talking, debating shared or differing views, trying something new (feather inlays with Fuzz Morgan at Conclave VII) and gaining the knowledge that we are all on the end of a phone or an email away when support is needed for that new rod building project. I am happy to openly admit that it is those very members who I share my “Legend” nomination with, as their support enabled me to enhance my lifetime rod building skills.
In the future I foresee the Guild growing in stature enabling members to enjoy all the benefits I have experienced. I hope to return to the USA to attend more Seminars, meeting old friends, making new friends, extending and sharing my rod building skills in the craft that is custom rod building.
My Step grandfather first taught me how to hand wrap rods in the late 60’s, mostly bamboo rods on a notched cardboard box and a phone book for a thread tensioner. I would do my own repairs and build an occasional rod over the years. I went to work as a sign painter working for 2 different uncles who were master sign crafters. When the computer industry started taking over the sign business I went to work as a cabinet finisher until the doctors told me after 25 years of breathing lacquer and other exotic finishing fumes I should quit or die young. I started a painting contracting business in the 90s, but really missed doing something creative. In 2004 I saw some pictures posted on bloodydecks.com of a few guys that were wrapping some really nice rods and decided to pick up where I had left off. The materials had all changed since the last rod I had done. With my background in exotic finishes it didn’t take long to get up to speed. I’ve found I can take a little bit from all my sign painting and cabinet finishing knowledge and incorporate it into design and building custom fishing rods and restoring and repairing old rods.
I was born into the sport fishing industry in 1963. My father had been running his own sporting goods store with a heavy emphasis on fishing and hunting since the latter part of 1955. So I was hanging around the shop from a very early age. There were always one or two guys working in the back doing rod and reel repair and basic custom rod building. I saw it being done even before I began taking a genuine interest. At the age of 12, I was helping my dad around the shop while he was in between firing and hiring new help and during the slow times began puttering around the work benches to fight away the boredom. It was then that my Pop noticed I was taking to rod wrapping like a duck to water. He never pushed me, but he certainly didn’t tell me I was wasting the thread. Let’s just say he nurtured it along.
By my mid teens I was doing work that was better than anything that had been associated with the business previously. I owe all my early advancements to all the books available at the time and later to all the publications by Dale Clemmens. It wasn’t long before I had talked my dad and his partner into investing in one of Dale Clemmens rod lathes, something I’m still working on to this very day, talk about a good investment.
I wanted to pursue a career in art, but I became a father and husband at the tender young age of 20, so art school became a dream that never came to fruition. So rod building became my sole avenue for any kind of an artistic outlet.
I ended up buying out my father’s 50% partner in 1989, and we ran the business as father and son until his death of cancer in 1992. I ran the business during the day and wrapped rods at night until I hired a couple of good men to run the business, while I built rods in a home workshop. My desire to focus on the rod building out weighed my desire to be a businessman. I ended up selling the business in 1997 and have been building rods as my main line of work ever since. It wasn’t until I began getting involved with other artists on the internet that my range of creatvity began to grow at quantum leaps. The young rod crafters out there have no idea what sharing online does for your education and growth in this craft. It’s an amazing tool we all have at our fingertips.
For the last 15+ years I have been a private contractor rod builder for various tackle shops around the San Diego area. I am making preparations to lauch my own business in early 2013 due to the numerous requests from my presence online the last couple of years. This is a very exciting time in my career and I thank the Guild for helping and supporting me over the last several months.
Regards,
Jim Trelikes
“The Art of the ROD……..to Seduce and Fish.”
My father took me fishing him when I was 8 and I caught my first fish on the Current River in Missouri. It was on a plastic worm and I was using an old rod and reel. My father always used a fly rod and was very good at catching fish on the Current River, a place I will always call home and the place I feel close to my father, even though he has since passed away. I visit the Current River a couple times a year and I can always feel his presence there with me. Dad always had time to take me fishing………
When I started rod building, it wasn’t long before I became bored. I knew there had to be more to rod building than turning down cork, placing guides Loomis IMX rod and adding a cheap Struble reel seat that did nothing to enhance the rod. So it wasn’t long, and I was looking for ways to not only make a better rod functionally, to make a better rod aesthetically.
So I began to look at rod building as I would fly tying, as a form of expression or functional art. When someone ties a fly to go fishing, they attempt to make it attractive to not only the fish, but to them as well. Many times I have seen fishermen refuse to use a fly that was ugly and not appealing to them. I look at rod building much the same way and if people find my rods appealing, they will buy them and use them, which is the ultimate goal is to have someone using one of my fly rods to catch fish.
I look at rod building as a form of art and expression for me. So when I began to build a rod, I look at it from the aspect of the beginning (the blank) to the end, that being the completed rod from the tip top to the reel seat. I start with a blank and even use the color of the blank as my canvas. Having the canvas, I then began to add components to make not only a functional piece of art, but for some of my customers to actually use materials in the rod such as feathers and different material inlays that make the rod part of them.
For me, I’ve always been able to see color and texture and when it comes to feather inlays, I somehow can place them aesthetically on a rod that is either appealing to people or represents something touching to an individual customer. Coupled with this, I include exotic materials on the handle that in no way limit the function of the rod, but enhance its look and appeal. I do the same thing with the reel seat and try to make the rod flow from the rod tip down to the reel seat and back again. Texture and feel of the feathers and a handle of my rods are the most important things to me. That is the guiding force on how I do inlays and are what inspire me to place the materials on the rod in the way that I do.
As a finishing touch to my rods, I also do custom guide spacing and test cast each and every rod prior to wrapping the guides. What I am able to do it is at times take stiffer rods and slow them down a little bit for the customer or take an IM6 blank and speed it up a little by lengthening the handle or using extreme lite wire guides to enhance the softness of an IM6 rod.
Rod building is an art form for me and is an expression of myself at times or is my interpretation of an expression presented to me for a customer. I know the things that I do to a rod are not accepted by everyone and that’s okay. I love to create….. I love to push the envelope….. I love to try new things….. and I LOVE TO FLY FISH!
I was raised in a military family and moved often. That bug remained with me and I have moved often in my adult life. Lived in Michigan until I was thirty and then moved to Alaska where I worked and played and earned my law enforcement retirement after twenty years . We lived in Montana from 2004 until April of 2012. Then we moved to our current home in Sequim Washington. In 2006 I took a position with a catering company which manages oil and gas camps and set up a security system for them. I was only going to do it for a couple of years, but it has now been six years. I have four more rotations of three weeks on and three weeks off to go and will resign and stay home to be with my wife and focus on rod building and wood working. I added a rod shop and a small wood working shop off my garage and look forward to becoming well acquainted with it. It will be great to be home full time and not live on a three week cycle. I am finding a lot of enjoyment, particularly, creating and turning cork and wood grips. I have been having some success at selling reel seat inserts and grips as well as complete rods.
While living in Soldotna AK. I took a community schools class on rod building thinking it would be a great way to build a good rod on the cheap. The craft bit me and 20 years later as I build myself another rod, between building for others, my wife will grin and say “Another cheap rod?”. I’m sure this in some aspect this is a familiar theme among my fellow rod builders. The class in Alaska was put on by George MacDowell of Mac’s Rod Shop in Soldotna AK. He was great teacher and motivated me to keep building, and my skill progressed from there.
I built a lot of Salmon and Halibut rods as well as fly rods in Alaska. During our years in Montana it was mainly fly rods while we lived in Lewistown and then Dillon. Now that I am on the Olympic Peninsula in Washington I look forward to building some larger diameter blanks which allow for more thread decorative wraps. It also offers me new fishing opportunities.
About three years ago I bought a small lathe and began turning my own cork and then wood grips and am now experimenting with inlays and accents. We never quit learning and since getting a laptop computer about three years ago, and learning to use it, I have found sites such as the Guild’s as well as Facebook (The NERB’s). I have met many builders and artists that eclipse my ability but are inspiring me to take chances and destroy some cork, wood and thread along the way, to improve my skill level and reach a point where I consider myself a professional rod builder. To be considered that by my peers, and earn respect from those who are masters of this craft is more than enough of a goal to keep one improving and aspiring to a higher level of craftsmanship. I will take this opportunity to close this and offer my very sincere Thanks to all those who have helped along the way and for the help and encouragement I continue to receive.
My name is Don Oehlke and I live in Wisconsin. My introduction to custom rod build began in the late 70’s when I built a couple of rods for myself and some friends. I was recently up north and saw a couple of the rods I built for some friends and relatives and have to admit they were really, really, really awful. I’d be embarrassed to even post them on any site. Then I went to a fishing expo in Madison, WI in February 2010 and to my amazement that I didn’t know at the time; I would meet Mark Blabaum and Al Hutchison. I really didn’t know if I wanted to reacquaint myself with rod building again but after looking at Mark and Al’s work the juices started to flow.
My background is in cabinet making so I was familiar with woods and how they looked in different situations. I was in awe of some of the handles Mark had done but I didn’t know how to approach him at the time to figure out how. About 4 months went by when I got a call from Al inviting me down to his house for a wood turning seminar put on by Mark and Bob Hasbrook. I couldn’t resist the invitation so I attended and was probably a thorn in poor Bob and Mark’s side as I really tried to pick their brains about how to do the different designs. That was all it took so when I got home I went overboard (much to my wife of 38 years dismay) and purchased the equipment I needed to do that type of work.
I have met so many people from the guild at the conclaves that have inspired me to push myself even further. It amazes me that there are so many rod builders that are willing to share their ideas with no strings attached. Since the conclaves Mark and I have stayed in touch and he has inspired much of my work in wood handles. Meeting B.D. Ehler at my first conclave and have him critique my work was awesome as he taught me so much. Ron Walter was inspirational in teaching me how to marble and e-mailing Doc Ski about weaving and having him answer plus critique my work made feel pretty good. I had the pleasure of meeting Billy Vivona in IA this last October and I can actually say he is quite a character and he inspired me to build a few EVA handles of which didn’t turn out too well but I’ll keep trying. Mark was also willing to show me how to program my own crosswraps in VisualWrap of which I have written some and am excited about wrapping. I have probably left a few people out that have inspired me and I truly apologize for that but believe me you are not forgotten. Hope you enjoy some of my work.
I grew up in Colorado in a family of fishermen. We spent every weekend and vacation fishing and camping in the beautiful Colorado Rockies. My mom’s father was an Engineer for the Rio Grande Railroad and brought coal to the Steel Mill in Pueblo. His schedule had him over-night in Salida where he had an apartment. He would fish the Rio Grande River where it ran through town every evening and was known in town as “Bill the fisherman.” So, I guess I inherited the genes that have led me to follow the fish throughout my life and to love anything that has to do with fishing.
I remember, as a teen, seeing a photo of a Chinook salmon in Outdoor Life magazine with a caption saying the fish was caught in a river in Alaska. To me it looked like a giant trout and I started dreaming of Alaska and fish like that. The dream became reality and I moved to Alaska in 1973 and ended up living on the very same river where that photo was taken years earlier (the Kenai River).
My other passion in life was art. I was always drawing, painting and doodling, so it was just a matter of time and probably inevitable that the two passions would meet. The cause of the meeting was a cheap factory spinning rod with wire guides that had been grooved by the line. I liked the rod, so decided to re-wrap it with better guides. I did the V-cut in the cardboard box thing with the thread passing through a large book for tension. It got the job done and that rod gave me a new passion. This was about 1976.
I bought a hand wrapper and a bunch of components from Netcraft (now Jahn’s Netcraft) and built my first rod from scratch. I even did a simple cross-wrap on it. By the time I’d finished that first rod I was fully immersed in a new addiction. Thirty-five+ years and about 3,000 fishing rods later my addiction has only grown. This will probably surprise you, but I’ve built every single one of those rods on basically the same hand wrapper. I’ve bought several over the years and I’ve modified them to fit my needs as my skills have advanced, but it’s still the same basic set-up. I’m dyslexic and left handed and power tools are never made for lefties, so I thought it better to avoid power wrapping.
I joined Rodcrafters and bought all of Dale Clemens’ books as they came out and with every rod I built I improved my skills. Also, every rod I built seemed to turn into another order as people liked the rods I was building and wanted one for themselves.
In the early 80’s I meet my wife, Silvia, who is originally from Costa Rica and on my first visit to that beautiful country I went on my first warm-water saltwater fishing trip. I was used to catching King Salmon in the 40 to 60 pound range on the Kenai and when I hooked-up with my first warm-water fish I thought I was fighting something of similar size, only to be amazed when a five pound yellowfin tuna came to gaff. Guess what – new passion!
We began to take one or two vacation fishing trips a year to Mexico’s Baja Peninsula and when I retired from the working world in 2002 we moved to the East Cape area of southern Baja, where we live today.
My rod building bench is located in our storage room which is not air-conditioned, so my rod building is limited to the winter months now days, as it’s too hot to work there in the summer. The fishing is too good in the summer to be working on rods anyway, so that is not a major problem. Now, instead of building a hundred rods a year, I’m building a couple dozen, but I’m enjoying every one as much as ever.
Bob Hasbrook, former President of the RodCrafters Guild passed away on Christmas Day, 2013. Pictured here are some of the rods he built including several award winning rods that were on display at the Guild’s North Central gatherings held at the St. Croix Rod Company in Park Falls Wisconsin. Bob was a quick learner when he joined the Guild and soon became fascinated with making beautiful wood handles with unique wood inlay work in exotic and complicated patterns of ellipticals, scallops, checkerboards, chevrons, diamonds, and other designs. His handle-making and thread work were always meticulous. His thread work always complimented his wood designs and he added what became his signature feather work on his most recent rods.
Bob was always proud of the fact that every rod he built got used on the water- and caught fish! Every June he brought all of the new rods he built over the winter on a Canadian fishing trip where they got a real workout. In fact two of his most beautiful award winning rods went over the side of the boat and were never recovered.
Bob also mentored other Guild members including Rich Wagner, his son Danny, his daughter Gracie, as well as me and my daughter Laura. In addition, Bob spent many hours teaching, demonstrating, consulting and providing technical assistance to his fellow rod builders on every facet of rod building.
His craftsmanship will live on……. in both the rods he built, and with those of us fortunate enough to learn from a true master rod builder.
by Kenny Lunquist – April 2014
Bob Batson started building rods in the living room of his home in Maui; principally to provide the means to support his family with the tools to provide their food through fishing. Others saw and wanted his rods which led to his opening the Phantom Custom Rods. His reputation continued to grow to where his custom rods were known as some of the best in Hawaii. He was featured in the television show “Fishing Tales” and in the book “Fishing Hawaiian Style.” Bob migrated to California where he worked for a prominent company until he took a leap of faith and opened the Batson Enterprise company in Sequim, Washington. Batson Enterprises was a founding Corporate Member of the Guild and supported the early annual conclaves and activities. Bob was widely recognized as the “moral compass” within the organization and was highly respected for his sterling standards of fair and ethical treatment of all. He believed in people and supported worthy causes for them. He openly shared his many custom rod building talents. Bob’s legacy will endure as an example of decency, caring, and sharing…and striving for the highest standards of quality in everything that he was involved.
/div
Bob McKamey a native of Shelbyville, Tennessee was one of the initiators of the custom Rod building world. He became a member of the Rod crafter’s organization almost at its inception. He attended some of the first meetings of this organization, starting in Huntsville Alabama. After attending his first meetings he was working with Lloyd Simmons, owner of Custom Rods in Shelbyville Tennessee, beginning his tenure at the ripe old age of 15. After working for several years with Mr. Simmons he had the opportunity to purchase the business and with Mr. Simmons strong encouragement he became the owner of the business.
During the early stages of the Rod Crafter’s, Bob served as a member of the group that did most of the organizing, planning and producing meetings in the southeastern part of the country. Working very closely with the original Rod Crafter’s, Bob was one of a small group of people that met to join the Rod Crafter’s and Custom Rod Builders Guide into one organization and became the first member of the new organization. He expanded the concept by organizing a regional concept known as the Duck River Event held in his horse barn.Eventually, Bob joined with Mudhole Rod Building and Tackle Crafting, where he is currently working.
Bob actually began his tenure building rods in his teens. As a member of Mr. Simmons Rod building and fishing tackle business, he started building custom rods for the public. During this time and after purchasing the business he spent many hours helping in the promotion of the custom Rod building. Bob McKamey continues to assist in the custom Rod building industry helping other people learn how to build a fishing rod. Seldom, did you visit his business or Mudhole when he is not actively assisting someone in building custom rods. Very few people, have provided as much total unselfish help as Bob McKamey, in the hobby/industry of custom rod building.
Bob is currently serving as the Senior Advisor to the President and the Board of Directors. In that capacity he is contributing to the recruitment of new members and expansion of more workshops and activities.
Al Goldberg was among the founding members of the Rodcrafters, formed by Dale Clemons. Al served on the Board of Directors and formed, then chaired the Northeast Region Chapter of the Rodcrafters. Over the years, Al has taught hundreds the art of custom rod crafting and has crafted thousands of creative rods. Al emphasizes the importance of the basics of rod building and their relation to making a rod meet the highest standards for which it intended to be used. His rods were balanced, perfectly aligned to the reel and line that were to be used, and then finished to the highest degree of perfection. Al shared his acquired abilities with others at regional and local workshops, Conclaves, and in many articles in the Rodcrafters Journal. He was personally responsible for introducting others who were later recognized as Legacy Legends to the Rodcrafter organization. The Legacy Legends Hall of Fame is not complete without the induction of Al Goldberg who ranks equal to those who were recognized long ago.
Garry Land graduated from the University of Texas Medical Branch in Galveston, Texas in 1971 with a medical degree and specialized in opthamology. He entered the Army as an officer and was first assigned to Fitzsimons Army Medical Center where he performed his medical residency. After leaving the Army as a Lieutenant Colonel, Garry, and his wife Sandy, settled in Clinton, Iowa were he started the Land Eye Center.
Garry first joined the Rodcrafters before the Custom Rod Builders Guild was formed. There hemet and has continued to maintain close friendships with many of the founding members of the Rodcrafters who later have become Legacy Legends in the Custom Rod Builders Guild Hall of Fame. He learned cross wraps and weaving BD Ehler and Doc Ski, guide placement and sensitivity from Don Morton, decorative techniques from Fuzz Morgan and Pat Vanzant, and instructional techniques from Al Goldberg. The Skills that he learned from those masters was not kept to himselff but, were shared with everyone that he met in the world of custom rod building.
Garry participated in virtually every capacity during his time as a Rodcrafter and continued to do so when that organization merged with the Custom Rod Builders Guild . He was on event committees that organized workshops and conclaves from the mid-west to the north and south east States. He often was the chairperson of those committees but never let thedemands of those duties distract him from also being a presenter on the event agaenda or sharing time in instructing individuals who sought his guidance.
After the Rodcrafters organization merged with the Guild, Garry became active as a volunteer to lead, or bea member of Guild committees regardless of the requirement. His reputation for not only being a dependable volunteer for whatever work needed to be done, but also for his high skills in virtually every aspect of rod building and organizational management accelerated his selection to lead projects, then to be a me ber of the Board of Directiors and soon afterwards to become the Vice President of the Guild. In fact, Garry occupied that position twice.
His first tenure as the Guild’s Vice President came during a period when the Guild was challenged by the development of rivalry conflicts withinthe growing rod building community, financial problems caused by poor decisions made during the merger of the two organizations, and the need for growth in corporate sponsors to meet the needs of the expanded size of the membership. Garry’s talent in leading people and managing organizations steered the Guild to resolve those issues and develop a smooth operational style to manage the Guild.
Garry has been a key player in event management, program development, and technical presentations at the local level workshopsand gettogethers for the Tri-State activities, his own annual workshop in Clinton, Iowa, those of organizationsi in Wisconsin and Minnesota, and the Guild’s regional events in Wisconsin, Illinois, Texas, and Florida. In addition, he has wrritten many articles for the Rodcrafter’s Journal that range from coverage of events, technical how to instruction, and special feature pieces o volunteer activities for youth, veterans, and special needs groups.
Garry Land has made a positive and indelible ark on the Guild through his generosity in sharing histime and talent in every aspect of the Guild’s operation. He is a true legend in the Custom Rod Building Guild and entire rod building community.
Curt Baker was born a rod builder. At a very early age he began tinkering with virtually anything that would look like a rod. Beginning with his grandfathers’ help, he used such things as pool cues, sewing thread and nail polish to fashion something called a fishing rod. A little later he was fortunate enough to have a shop teacher that honed his interest in actually building a fishing rod. This start allowed him to learn enough to begin building a real custom rod. With this start, he began working diligently to hone his skills in building fishing rods and developing new better techniques to produce much higher quality rods.
Living in St. Pete and having Tampa Bay very close at hand, he began to develop a strong interest in fishing and in building fishing rods. The interest in building fishing rods and working with friends in the establishment of an interest in building fishing rod, he formed a group of like-minded individuals that adopted the name of Suncoast Rodcrafters. His group gained, first, a local interest that soon expanded throughout the easterrn US region. Many rod builders traveled great distances to experience thefriendlyworkshop atmosphere off Curt’s organization. Meeting on a weekly basis the improvement in the art and craft of rod building was shared among the attendees. Curt and the group of Suncoast Rodcrafters became involved with the Rod Crafter’s during meetings in the Orlando area. This venture proved to be extremely valuable to both the Suncoast Rodcrafters and the Rod Crafter’s and later the custom Rod Builders Guild. The joining of these two groups provided very valuable exchanges of ideas, techniques and procedures that prove extremely helpful to both groups. This model is one that can be replicated in a number of different ways to greatly enhance the world of custom Rod building.
Curt has been extremely influential in presenting new ideas, techniques and procedures to not only local clubs, but also to national and international groups. He is sought out as a presenter in virtually all of the workshops and seminars and has disseminated vast amounts of custom Rod building information and establishing a model of organizations that can produce the sharing of information His model can easily be replicated and serve as a guide for establishing other clubs and organizations. Curt is the senior instructor for Mudhole. He provides instruction to beginning rod builders as well as advanced topical subjects to those with established advanced skills. His subjects are diverse and include cross wraps, weaves, marbelling, inlays, as well as innovative technologies such as laser engraving and the application of new materials. Curt is the epitome expert instructor, organizer, and leader in promoting and advancing the skills of custom rod crafting.
Jerry Jenkins is a rod builder many of us have come to know as the man who travels the farthest to rod building events. He is from Anchorage Alaska. Jerry became a member of the Guild in 2014. He attended his first event at Dallas / Fort Worth in March of 2016.
Since that time, Jerry has been a very frequent contributor of articles to the Rodcrafters Journal including several covers on the Journal. Jerry is a regular instructor at several regional events. He is passionate about passing on his skills and rod building knowledge which is the purpose of the Guild. He challenges you to become a better rod builder and yet he is always there to learn new skills. Jerry has served as a director of the Guild including helping with the Youth Mentorship Program. He has mentored children from both Alaska and Wisconsin.
Many rod builders learn their skills from other rod builders. Very rew have skills they can say that they have invented. The one thing that sets Jerry apart from many rod builders is his invention of embeded lettering in cork and EVA rod handles. To this skill, Jerry has added multiple diamond layers for which he has earned the title, “The King of Diamonds.” Jerry is so dedicated to rod building that he has a second rod building shop at his “cabin”i Idaho where he escapes part of the Alaska winter.
Jerry is a very generous individual. He is always giving people things, especially when it comes to rod building, often before they know that they need it. Jerry contributes completed fishing rods to organizations for fundraisers.
Jerry Jenkins deserves the recognition of being added to the Legacy Legends Hall of Fame for both his service to the Custom Rod Builders Guild and his outstanding achievements and innovations in rod building.
Archie McCarty is an ultimate spokesman and team player for the craft of custom rod building. In 1998 he began making cedar wood rod handles that he personally turned on a wood lathe at his home. Quickly demand for his handles grew and pushed his basic design to shapes for spinning, casting, fly, split grips, and ice rods. Although he opened a website to advertise his handles, he does not own or use a computer. That, alone, says much about Archie McCarty’s character! He does not use a computer because he wants to talk with people instead of using impersonable electronic communications. And he is as likely to give someone his excellent handles as to sell them one. Archie has given countless numbers of his handles to schools, clubs, veterans, to charities. He has donated handles to the Guild’s Youth Membership annual rod competitions for both the provided rod components and as for prizes given to every contestant.
Archie has participated in virtually every Guild workshop and local event in the North Central Region, and is a regular exhibitor in the annual International Custom Rod Builders Exposition. He is the organizer and sponsor of the annual Minnesota Rod Builders gathering as well as participates in other North Central Regional Guild and local events to include the Tri-State workshop, Wisconsin Rod Builders Get Together, Sturgeon Bay gathering, and the St. Croix/Park Falls workshop. Archie volunteers to be a Guild Ambassador at local events where he shares the mission, activities, and benefits of Guild membership with the event participants. He has been a workshop presenter and contributor of numerous Rodcrafters Journal articles. Archie has been a silver tier level Corporate Member of the Custom Rod Builders Guild for two decades.
Don Shafar is a visionary “difference maker.” He looks beyond the status quo for better possibilities and selflessly works to make them happen. Has been a committee member for the planning, organization, and operation for numerous Guild workshops. In addition to his assuming important committee responsibilities, he has been a presenter, raffle manager, treasurer, registration receptionist, and member of the set-up crew; he checks off every area on a “how can you help” pre-event volunteer survey.
Don has been a member of the Rodcrafters Journal editorial committee as a planner, contributor scout, and theme designer. His insights in the use of social media to ascertain the interests of the membership have contributed to keeping the Journal’s content fresh and relevant. Don has contributed many articles and photographs for the Journal to include cover, centerfold, and Member’s Spotlight pictures. His photographs demonstrate that his artistic talents go far beyond the masterful craftsmanship of his rods. They are compositions of fore and backgrounds, light, and focus that emphasize the quality of his work.
Don’s rodcrafting skills are extraordinary. He has won multiple People’s Choice Awards in Guild workshops; was a finalist in the International Rod Building competition, and showcased at the International Custom Rod Builders Exhibition.
Don pared his expertise as a professional automotive and industrial equipment painter with his rodcrafting. Demand for his artistic rod painting grew rapidly and caused him to have to decide to pursue either his commercial employment or his rod painting. He chose the latter and launched the Backbone Custom Rods business with advertising on multiple social media platforms. At the same time, he elevated his personal Guild membership to become a Silver tier level Corporate Member. Don continues to push the envelope of rod painting designs. He researches colors to exact standards as often registered by universities, fraternities, professional organizations, military and first responder associations. He has a growing catalog of fish patterns that cover virtually every common fresh and saltwater sport species as well as many exotic and tropical varieties. Don’s schemes include subtle color transitions, patriotic tributes, graphic representation of flames, lightning, and even wood grain. Don partners with other Guild Corporate members to obtain the custom blank and components desired by his customers and then paints them to the artistic scheme of the order. Don has become the ultimate expert source for design and painting of custom rods.
Al has been the past president of the guild and has been active in the guild for approximately 20 years.
He has been involved in teaching hundreds and hundreds of kids and adults over the years, and for the last few years has been mentoring youth in the Guilds youth rod building program. All this and has helped many individuals at his home, and runs the Wisconsin rod builders meetings every year.
Over the more than a decade that John Sturm has been a member of the Custom Rod Builders Guild he has set a pace that few others can rival. He was the Director of Corporate Membership on the Board of Directors. During his tenure he developed a spreadsheet with embedded macro management tools that quickly became the standards used by the other Board of Director membership managers. Those tools included early notifications of approaching renewal dates, invoices and contracts, acknowledgement letters, and thank you letters. The three succeeding Corporate Membership Directors followed John’s management procedures without change.
John has had numerous cover, center fold, and Member Spotlight photos of his exquisite rods in the Rodcrafters Journal. Additionally, he has written articles that covered techniques for cross wraps, rod repair, shop set ups, and tribute rods. He prepared a series of videos that covered the steps in building a rod. That instructional series is included in the How To section of the Guild’s website.
John has been a featured presenter at many Guild and local workshops in the South East and North Central regions. His subjects covered basic and advanced cross wrap techniques, laser engraving, and decorative techniques using acrylics and wood.
John won three consecutive People’s Choice Awards at the St Croix workshop in Park Falls, WI. He mentored two youths in the Guild’s Youth Membership program, and each won first and second place in the first two annual rod competitions. John is also a registered Guild mentor and has assisted members who sought assistance with advanced cross wrap techniques.
John Sturm has set high standards for others to emulate – both personally and as a professional manager. He has shared his expert level skills with others in workshops and in mentoring programs. He has been a leader as well as a strong team member on committees and the Board of Directors. He has been a prolificate contributor to the Rodcrafters Journal and the How To website section.